|
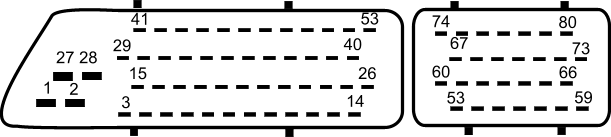 |
1 |
Upstream oxygen sensor heater – output |
2 |
Down stream oxygen sensor ground – input |
3 |
Downstream oxygen sensor supply – output |
4 |
CKP sensor supply – output |
5 |
CMP sensor ground – output |
6 |
Oil temperature sensor ground – input |
7 |
ECT sensor ground – input |
8 |
MAP sensor supply (5V) – output |
9 |
Differential speed sensor signal (EM-CVT gearbox) - input |
10 |
Oil temperature (VVC only) - output |
11 |
Not used |
12 |
Decrease solenoid valve (VVC) - output |
13 |
IAC valve stepper motor phase B - input/output |
14 |
Injector 3 ground - input |
15 |
Upstream oxygen sensor supply - output |
16 |
CMP sensor signal - input |
17 |
CKP sensor ground - input |
18 |
IAT sensor ground - input |
19 |
Main relay supply signal - input |
20 |
TP sensor signal - input |
21 |
Engine bay temperature sensor signal - input |
22 |
Not used |
23 |
Not used |
24 |
IAC valve stepper motor phase D - input/output |
25 |
Injector 1 ground – input |
26 |
Ignition coil 2 ground – input |
27 |
Downstream oxygen sensor heater (2001 MY onwards) - output |
28 |
Upstream oxygen sensor ground - input |
29 |
Downstream oxygen sensor negative (2001 MY onwards) - input |
30 |
CKP sensor negative – input |
31 |
MAP sensor ground – input |
32 |
Engine oil temperature sensor signal - input |
33 |
ECT sensor signal – input |
34 |
TP sensor ground – input |
35 |
Alternator load signal – input |
36 |
Not used |
37 |
Sensor ground – input |
38 |
EVAP purge valve drive – output |
39 |
IAC valve stepper motor phase A - input/output |
40 |
Injector 4 ground - input |
41 |
Upstream oxygen sensor negative - input |
42 |
CMP sensor ground |
43 |
Not used |
44 |
IAT sensor signal - input |
45 |
MAP sensor signal - input |
46 |
TP sensor supply (5V) |
47 |
Not used |
48 |
Instrument pack - gearbox position display PWM signal - output |
49 |
Increase solenoid valve (VVC) - output |
50 |
IAC valve stepper motor phase C - input/output |
51 |
Injector 2 ground - input |
52 |
Ignition coil 1 ground - input |
53 |
A/C clutch relay coil ground - input |
54 |
Main relay coil ground - input |
55 |
Instrument pack - tachometer drive - output |
56 |
A/C trinary switch hi/low - input |
57 |
Not used |
58 |
Diagnostic K line - input/output |
59 |
Main ground 1 - input |
60 |
Cooling fan relay coil ground - input |
61 |
Ignition switch - input |
62 |
Instrument pack - engine bay overheat warning lamp - output |
63 |
Park/neutral switch - input |
64 |
Rough road sensor positive (non ABS) - input |
65 |
Not used |
66 |
Main ground 3 - input |
67 |
Cooling fan relay 1 coil ground - input |
68 |
Fuel pump relay coil ground - input |
69 |
MIL lamp (2001 MY onwards) - output |
70 |
Trinary switch A/C fan request - input |
71 |
Sensor ground - input |
72 |
Alarm ECU - immobilisation coded signal - input |
73 |
Main ground 2 - input |
74 |
Engine bay cooling fan relay coil ground - input |
75 |
Gearbox interface unit data receive (EM-CTV gearbox) - output |
76 |
Not used |
77 |
Gearbox interface unit data receive (EM-CTV gearbox) - input |
78 |
Road speed signal - input |